Tồn tại một vấn đề âm ỉ trong việc cải tiến Lean. Đó là tỷ lệ thất bại cao ngất ngưởng trong quá trình cải tiến. Vậy tại sao việc cải tiến lean lại gặp nhiều thất bại như vậy? Đã đến lúc chúng ta phải suy ngẫm sâu sắc hơn về vấn đề này.
Ban đầu, Lean được dựa trên Hệ thống Sản xuất Toyota (TPS). Theo thời gian, nhiều điều đã được bổ sung vào các phương pháp thực hành Lean, và Lean đã có nhiều ứng dụng hơn chứ không còn như hồi sơ khai ở TPS nữa.
Vào năm 1994, nhà máy lớn nhất của Toyota và là nhà máy ô tô lớn thứ hai trên thế giới, Toyota Motor Manufacturing – Kentucky (TMMK), đã hợp tác với Đại học Kỹ thuật Kentucky để giảng dạy các nguyên tắc của Hệ thống Sản xuất Toyota. Ban đầu, họ gọi chương trình là “Lean”, nhưng sau đó lại đổi tên thành “True Lean”. Lý do họ đổi tên như vậy là để phân biệt hệ thống Lean mới với nhiều thay đổi phù hợp hơn với Hệ thống sản xuất Toyota ban đầu. Website của họ nêu lên nhiệm vụ của chương trình “Là khám phá, nghiên cứu và giảng dạy một cách có hệ thống các hoạt động của TPS. “True Lean” là một hệ thống. Nó không chỉ là Toyota Kata, hoặc Six Sigma, hay là một công cụ.” Ngoài ra còn một công cụ khá là phổ biến ở trong Lean đó là sơ đồ chuỗi giá trị (VSM).
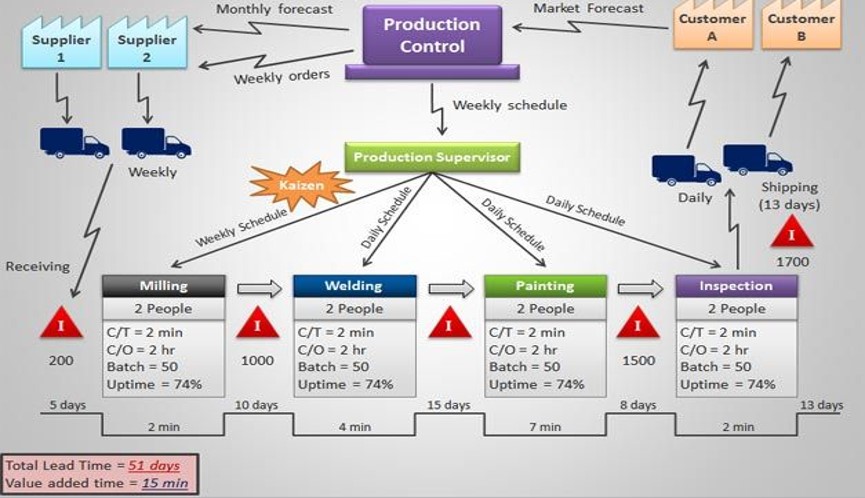
Cách đây nhiều năm, Fujio Cho – cựu Chủ tịch Tập đoàn Ô tô Toyota đã nói trong Phương thức Toyota rằng: “Nhiều công ty sản xuất của Mỹ đã áp dụng thực hành kaizen và các công cụ TPS khác. Nhưng tất là chỉ được làm riêng biệt, tách lẻ và không hề có tính thống nhất. Điều quan trọng là phải tập hợp tất cả các yếu tố cùng nhau thành một hệ thống. Nó phải được thực hành hàng ngày một cách rất nhất quán – không bộc phát – một cách cụ thể trong nhà máy. ” Chỉ trong một vài câu, ông Cho đã xác định được sự khác biệt giữa Hệ thống Sản xuất Toyota và những hệ thống tinh gọn khác của các công ty Mỹ.
Hệ thống mà Cho tham chiếu là hệ thống Just-in-Time của Toyota, và khẳng định tầm quan trọng của nó không thể bị thay thế trong TPS. Taiichi Ohno, Cha đẻ của TPS, tin rằng hệ thống Just-In-Time của Toyota là một “lợi thế sản xuất” của Toyota đối với các đối thủ cạnh tranh. Trên thực tế, trong nhiều năm, ông không cho phép lưu truyền bất cứ điều gì về hệ thống JIT của Toyota! Yasuhiro Monden, tác giả của Hệ thống Sản xuất Toyota: Phương pháp Tiếp cận Tích hợp để thực hiện Just-in-time , đã nói rằng “Tính năng quan trọng nhất của TPS là JIT… JIT là phần trung tâm của TPS.”
Monden và Ohno tin tưởng vào tầm quan trọng và lợi thế của hệ thống JIT của Toyota vì nhiều lợi ích mà hệ thống này mang lại. Những lợi ích mà JIT mang lại có thể kể đến: quy trình làm việc đồng bộ và nhịp độ, giảm chi phí lao động và hàng tồn kho, cải thiện thời gian sản xuất, tăng năng suất, chất lượng tốt hơn và tăng thời gian giao hàng đúng hạn.
Trong The Birth of Lean, Koichi Shimokawa và Takahiro Fujimoto có đề cập rằng TPS là “phát triển dần dần, từng bước một”. Những người sáng lập đã đóng góp các yếu tố của hệ thống và làm việc không ngừng nghỉ để triển khai chúng. Nhưng không ai định hình và hình dung ra khuôn khổ TPS là như thế nào: “Họ chỉ đơn giản là giải quyết từng vấn đề nảy sinh tại nơi làm việc, từng giải pháp của họ được tích lũy và dần dần trở thành cái mà chúng ta ngày nay gọi là Hệ thống sản xuất Toyota”.

Vào năm 1956, trong một chuyến thăm Hoa Kỳ, Ohno đã thấy cách các cửa hàng tạp hóa hiện đại của Mỹ sử dụng phương pháp mà ngày nay chúng ta gọi là phương pháp kéo (Pull System). Ohno đã áp dụng phương pháp này và sử dụng các công cụ và phương pháp của TPS để có thể phát triển, nâng cao và bổ sung cho nó. Trên thực tế, chính Ohno đã nói rằng heijunka và kanban là biện pháp đối phó với các vấn đề gặp phải. Họ đã “giải quyết các vấn đề nảy sinh” bằng cách sử dụng phương pháp kéo.
Không có gì phải bàn cãi khi cho rằng Hệ thống sản xuất Toyota (TPS) là tiêu chuẩn vàng cho sản xuất chi phí thấp, chất lượng cao, thời gian ngắn. Tinh gọn dựa trên Hệ thống sản xuất Toyota và hệ thống JIT vừa là “tính năng quan trọng nhất và là bộ phận trung tâm của Hệ thống sản xuất Toyota” vừa là “lợi thế sản xuất”đối với Toyota. Nhưng tại sao việc cải tiến Lean lại thất bại thường xuyên như vậy?
Có nhiều nghiên cứu học thuật về lý do thất bại của Lean. Một nghiên cứu về lý do thất bại của Lean đã được xuất bản vào tháng 2 năm 2016 bởi Tạp chí Quốc tế về Quản lý Chất lượng & Độ tin cậy (International Journal of Quality & Reliability Management.)
Nghiên cứu xem xét một cách có hệ thống 56 bài báo học thuật nổi tiếng được xuất bản về Lean, Six Sigma từ những năm 1995 đến năm 2013. Trong nghiên cứu, 34 yếu tố thất bại đã được xác định. Không có lý do thất bại nào trong số này có liên quan đến cam kết đầy đủ và triển khai hệ thống Just-In-Time.
Với một mớ hỗn hợp các công cụ, phương pháp và cách tiếp cận, người ta sẽ nghĩ rằng: “Liệu một trong những công cụ này sẽ hoạt động, phải không? Liệu Agile, 6-Sigma, Lý thuyết ràng buộc (Theory of Constraints), Bản đồ dòng giá trị (VSM), Kaizen, hay thứ gì khác có thể đạt được thành công không? Mặc dù cải thiện ngắn hạn trong một số lĩnh vực có thể xảy ra, nhưng kết quả không đạt được hiệu quả như hệ thống Just-In-Time của Toyota. Trên thực tế, đống hỗn tạp các công cụ, phương pháp này là vấn đề khi xảy ra thất bại trong quá trình cải tiến.
Trong cuốn sách Taiichi Ohnos Workplace Management của mình, Taiichi Ohno đã nói: “Quá khứ chỉ là quá khứ và điều quan trọng là tình trạng hiện tại và những gì chúng ta sẽ làm tiếp theo để vượt ra khỏi vị trí của ngày hôm nay.”
Vậy, chúng ta nên làm gì “để vượt ra khỏi vị trí của chúng ta ngày nay”?
Bảng xếp hạng tinh gọn hiện tại không dựa trên hệ thống Just-In-Time của Toyota. Để khẳng định cho điều này, có một số yếu tố riêng lẻ của TPS như SMED, 5S, Giải quyết vấn đề theo 8 bước và TPM có thể được thực hiện mà không cần giải quyết phương pháp sản xuất. Nhưng những phương pháp cải tiến này không phải là kết quả của hệ thống sản xuất Just-In-Time. Chúng không cần phải quá liên quan đến JIT.
Chúng ta hiểu được tầm quan trọng của hệ thống JIT của Toyota và giá trị của nó. Chúng ta cũng biết những gì Toyota đã phải làm để có được hệ thống JIT hoàn chỉnh như này nay. Vậy nên, ngay từ bây giờ doanh nghiệp nào cũng nên xây dựng và có một hệ thống JIT của riêng mình và hãy lấy nó làm “lợi thế sản xuất ” này cho doanh nghiệp của mình.